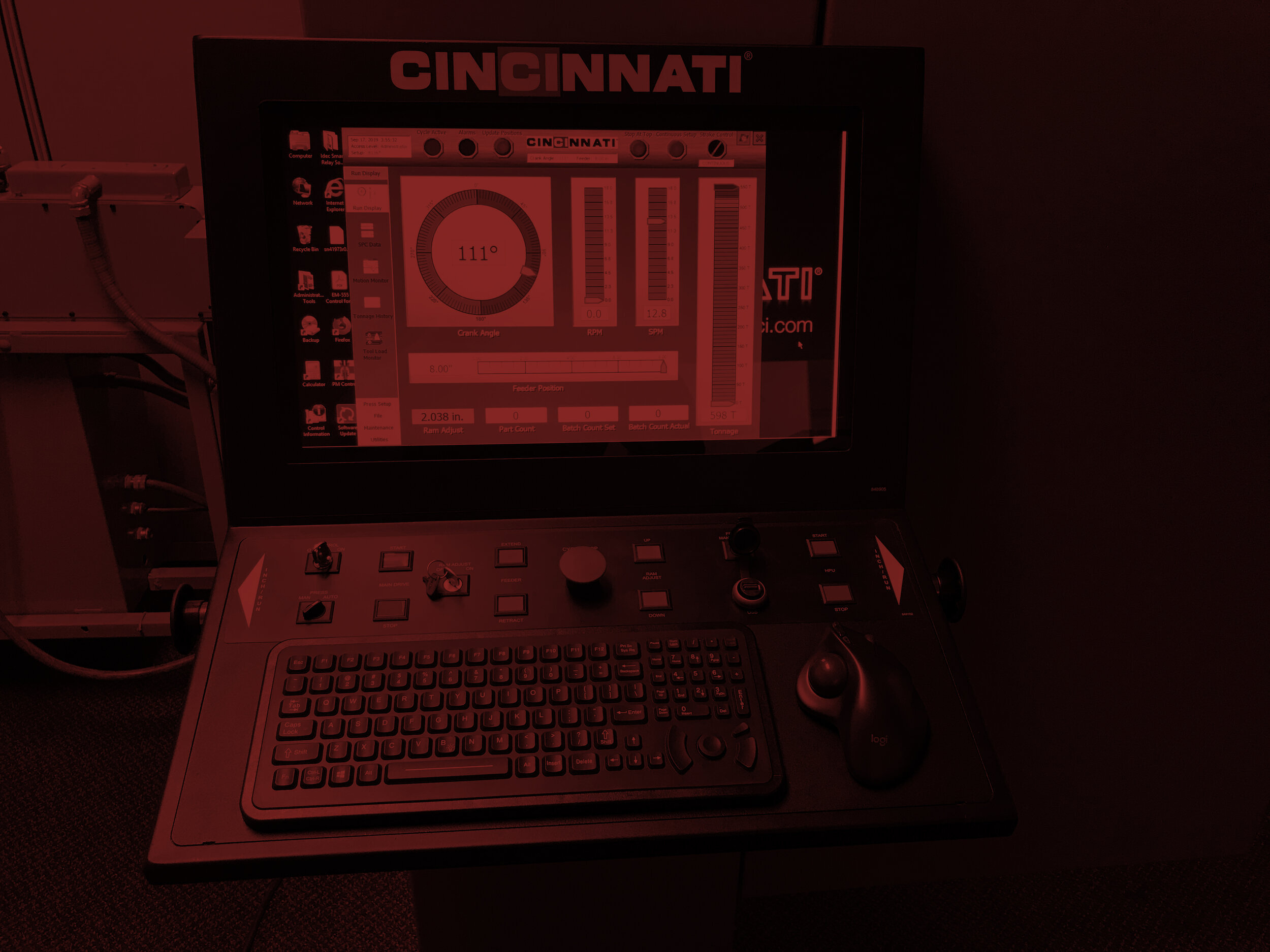
Power Die Change
Power Die Change Presses dramatically speed job changeover allowing die sets to be changed in less than 10 minutes. This makes the CI PDC ideal for small-lot processing.
Power Operated Die Set Transfer System
Die Sets are exchanged in a matter of minutes using the power operated die set transfer system. Each die set maintains full time utility connections to speed exchange and provide a means to simulate press motion during tooling set-up. A power-operated hoist is provided to assist tooling installation/removal and is large enough to use for major die set repairs if necessary. A moving floor system increases operator access during tool changes and keeps unwanted debris out of the press pit.
CINCINNATI® follows the policy of continuous advancement in product development. For this reason, specifications and dimensions are for reference only and can change without notice. Foundation plans are furnished with each new machine installation.
Features | 440-DC3-6 | 880-DC3-7 | 1650-DC3-8 |
---|---|---|---|
Die Set | ![]() |
![]() |
![]() |
Main Ram Pressing (tons) | 440 | 880 | 1650 |
Productivity (SPM) | 6-18 | 5-15 | 6-12 |
# Of Pressing Levels Upper* | 3 | 3 | 3 |
# Of Pressing Levels Lower* | 5 | 5 | 5 |
Fill Depth (in) | 6 | 7 | 8 |
Die Opening (in) | 15-5/8 | 15-5/8 | 26 |
Platen Ejection Capacity (tons) | 150 | 200 | 500 |
Core Rod Ejection Capacity (tons) | 19 | 19 | 35 |
Feeder Opening (in) * | 9 | 9 | 12 |
Main Ram Tonnage Monitoring | ![]() |
![]() |
![]() |
Platen Motion Monitoring | ![]() |
![]() |
![]() |
Platen Tonnage Monitoring | ![]() |
![]() |
![]() |
SPC Data Collection | ![]() |
![]() |
![]() |
Main Ram Tonnage Monitor | ![]() |
![]() |
![]() |
Programmable Feeder | ![]() |
![]() |
![]() |
Powder Hopper(s) | ![]() |
![]() |
![]() |
Top Punch Holddown | ![]() |
![]() |
![]() |
Allen Bradley Control | ![]() |
![]() |
![]() |
Touchscreen HMI | ![]() |
![]() |
![]() |
Remote Diagnostics | ![]() |
![]() |
![]() |
Machine Commissioning & Training | ![]() |
![]() |
![]() |
*Options May be Required
Key Features
-
Hybrid Press Design
The CINCINNATI Power Die Change Compacting Press combines the speed and accuracy of a mechanical press with the controllability of a hydraulic press. This unique combination is the solution for lean manufacturing pressing requirements of complex precision PM parts.
-
Multi-Level Part Capability
Complex PM parts with up to 8 levels can be produced on a CINCINNATI Power Die Change Compacting press using the following independent tooling levels: Outer Upper Punch, Middle Platen Punch, Inner Upper Punch, Shelf or Straight Through die, Outer Lower Punch, Middle Lower PunchInner Lower Punch, and Through, Stepped or Blind Core Rod.
-
Unique "Tri-Press Stops"
Outer and Middle Lower Punches are supported on "Tri-Press Stops" to facilitate production of complex parts that generate off-center loading. The combination of three press stops per platen and robust guiding ensure production of precise parts using tight tolerance tooling.
-
CINCINNATI Press Control Center
Operator-oriented fingertip programming control is provided to simplify press set-up and operation. This powerful control not only provides basic control of the press, but also performs extensive press and process monitoring. With available options, it can make on-the-fly process changes to reduce part-to-part variability within a production run.
-
CNC Platen Motion Control
Critical Platen motions are established by generation of a Desired Motion Trace using basic part information. The color display indicates the programmed and actual traces of each lower tooling member. This speeds part development and facilitates part problem identification.